Article/Clean Containers for High‑Purity Chemicals: Ideal for Storage and Transport
High‑purity chemicals are essential in semiconductor manufacturing and electronic materials. To maintain quality throughout storage and transportation, selecting the right clean containers is crucial. “Clean containers” are produced in controlled environments with low particulate levels and use materials that minimize leaching of metallic or other contaminants. Below, we explain why clean containers are key to preserving purity in chemicals and how to choose them.
Characteristics & Challenges of High‑Purity Chemicals
High-purity chemicals must maintain extremely high levels of purity, as even minute impurities can significantly affect product quality. Consistent quality control throughout the entire process—from production to final use—is essential.
・Contamination control
Even trace impurities can compromise product quality. Choose containers with excellent sealing and minimize exposure by handling them in clean environments.
・Environmental sensitivity
High‑purity chemicals often react to changes in temperature, humidity, or light. Proper environmental controls are necessary during storage and transport.
・Vibration and impact resistance
Movement during transport can jeopardize chemical integrity. Containers made from shock-resistant materials and compliant with UN regulations help safeguard contents.
How to Choose Clean Containers
1.Material compatibility
Select container materials that are chemically inert with the stored chemical, and that do not leach into the contents.
2.Particulate control
Containers should be manufactured in low‑particulate environments. Depending on the chemical, containers may also be pre-washed before use.
3.Design & structure
Look for features like airtight lids, structural strength, ergonomic handling, and designs that minimize residuals. For hazardous chemicals, ensure the container meets UN transport standards.
4.Size and capacity matching
Match container size to your needs—whether lab-scale or production-scale. Using the same material for R&D and scale-up can streamline container validation and reduce lead time.
Sekisui’s Clean Container Solutions
1.High-grade polyethylene materials
Sekisui’s inner linings use polyethylene with minimal metal leaching, offering strong resistance to various chemicals.
2.Strict particulate control
In Sekisui’s clean manufacturing facilities, cleanliness is tightly monitored. For example, 200 L clean drums are produced in environments where ≤ 10 particles ≥ 0.5 µm per mL are present
3.UN‑rated designs & low leftover volumes
Sekisui offers a complete lineup—from sub‑1 L clean bottles to 200 L drums—all compliant with UN hazardous‑goods shipping standards. Expert design helps reduce residual liquid and improves user efficiency .
4.100% renewable energy production
Sekisui’s facilities are transitioning toward renewable energy to reduce greenhouse gas emissions. Full production using 100% renewable electricity is planned starting April 2025 .
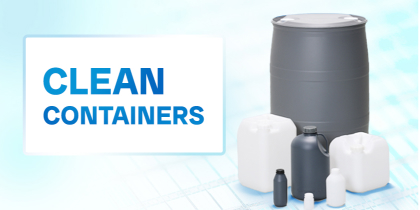
For more detailed information tailored to your application—whether you’re working in labs or large-scale manufacturing—feel free to get in touch for inquiries